Enhancing workplace safety is crucial, particularly when it comes to material handling operations involving forklifts. Forklift accidents can result in severe injuries and fatalities, making it essential for facilities to prioritize safety measures. By regularly inspecting and maintaining five critical forklift safety devices, businesses can significantly reduce injury rates and create safer working environments.
1. Brakes
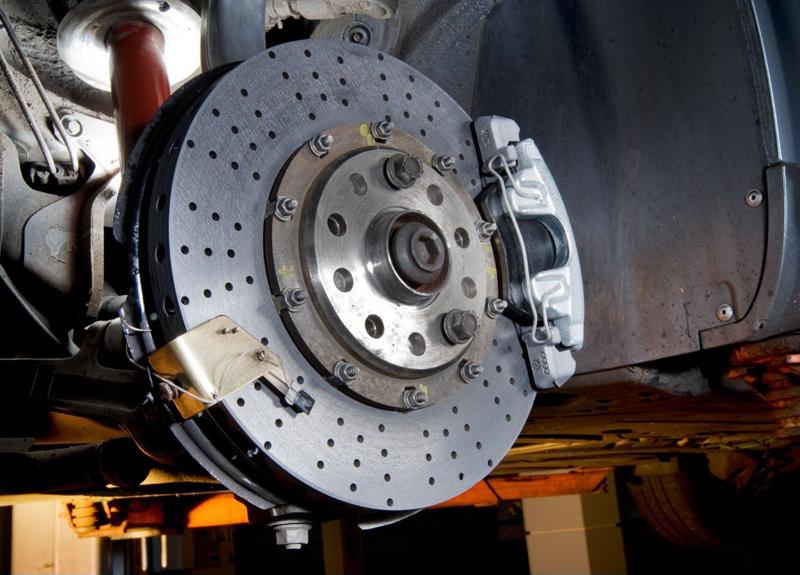
Forklift brakes should be fully functional anytime the truck is used.
2. Seatbelts: Upholding Operator Security
According to OSHA Director John B. Miles, Jr., all powered industrial lift trucks manufactured after 1992 must be equipped with a restraint system or enclosure. Seatbelts play a crucial role in preventing tip-over accidents, which are among the most common incidents involving forklifts. Operators should always wear their seatbelts and follow safety protocols in the event of a potential tip-over. Regular inspection and maintenance of seatbelts are necessary to ensure they serve their vital purpose in operator safety.
3. Overhead Guards: Protecting Against Falling Objects
While overhead guards shield operators from falling objects, it's important to note that they are not designed to withstand the impact of a full load. Operators should wear appropriate personal protective equipment, such as hard hats, in addition to relying on overhead guards. Daily inspections are crucial, and any signs of damage, including dents, broken welds, or missing bolts, should result in immediate decommissioning and repair of the forklift.
4. Lights: Communicating Safety Messages
Lights on a forklift serve as important communication tools with other individuals in the vicinity. Alongside mandatory brake lights and headlights, forklift safety lights may include directional lights, flashing warning lights, and blue safety lights. Compliance with OSHA's lighting requirements, particularly in areas with low general lighting, is essential. Regular maintenance and inspection of these lights are necessary to ensure their effectiveness.
5. Horn: Alerting Others for Enhanced Safety
Noise can be a valuable safety instrument. OSHA mandates that all forklift operators have access to an operator-controlled horn, whistle, gong, or another sound-producing device. These devices help alert people nearby to the forklift's presence and movements. Operators should sound the horn at blind corners or intersections with limited visibility. Furthermore, backup alarms that activate when the forklift is operated in reverse contribute to worker awareness.
Maintenance Services for Optimal Forklift Performance In addition to the aforementioned safety devices, proper maintenance of personal protective gear, fire extinguishers, and other safety assets is crucial in minimizing accidents. National Maintenance Services can help ensure your industrial trucks are in top condition. We provide dedicated on-site technicians who work diligently to maintain and repair your assets, enabling a safer work environment.
Prioritizing forklift safety is paramount to protecting employees and minimizing accidents. Regular inspection and maintenance of crucial safety devices, including brakes, seatbelts, overhead guards, lights, and horns, significantly reduce the risk of incidents. Partnering with National Maintenance Services guarantees expert maintenance services and heightened workplace safety.
Contact our on-site maintenance department today to safeguard your business and employees.