While the holidays may mean family gatherings and workplace parties for most people, for the average facility manager, it means busy days are ahead.
Peak season always brings challenges, but there are plenty of ways to plan ahead so you can skillfully handle the busiest weeks of the year. Have you considered how you manage your rental equipment during peak season? Here are eight ways to get the most out of your assets this holiday season:
1. Review last year's obstacles
Look back at records from peak seasons past to see what challenges you faced. If you identify a pattern, like more forklift malfunctions than usual or bottlenecks at packaging stations, start thinking about a solution before business picks up. Do you need to schedule in-depth forklift inspections and repairs or all-out replacements? Were there a couple weeks where extra lift trucks would have helped? Strategic equipment rentals can help you avoid these challenges, but only if you know exactly how you want to use them. Your peak season track record will let you know.
2. Do a trial run
When your busiest days happen at the same time every year, it's easy to forget the many demands that come with them. The best way to prepare and weed out obstacles is to practice.
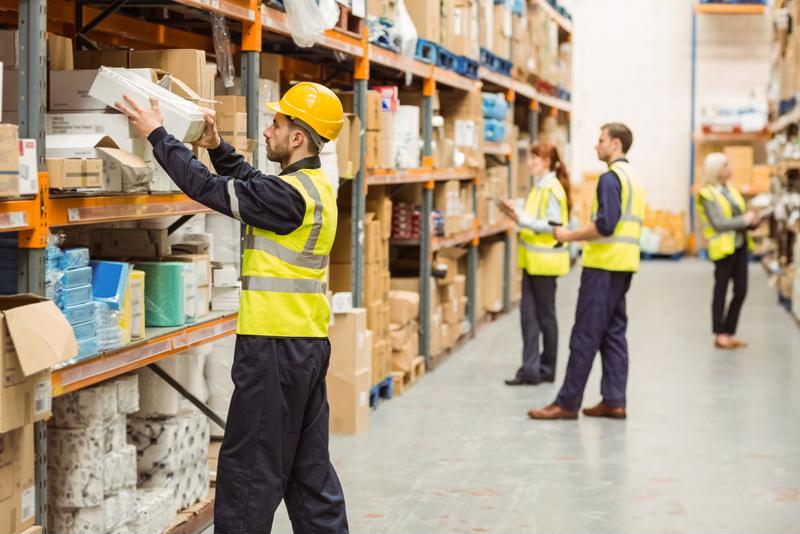
Surge testing can help you identify problem areas before peak season ramps up.
Inbound Logistics recommended holding a trial run by performing surge testing. To do this, hold up a half-day's order volume, then attempt to get through the entire day's work in a four-hour period. This will give you a good idea of what a heavy influx in orders will feel like, and lets your employees get into a rhythm for faster days. If you do decide to rent extra equipment to meet holiday demand, it'll also give your employees an opportunity to familiarize themselves with anything new and unfamiliar about the models you leased.
3. Swap out unreliable equipment
During peak season, you need to know that you can count on all your equipment to work correctly. If you have unreliable equipment, now is the time to repair or replace it. If you're not sure which pieces of equipment can't be counted out, it may be time to invest in a Computerized Maintenance Management System. A CMMS compiles data like maintenance request histories and usage patterns to help identify patterns among your fleet.
If your current material handling equipment isn't operating at peak efficiency, the holiday rush won't help matters. Instead of investing in new equipment now, consider renting. Doing so will provide a low-cost understanding of just how much material handling equipment you need to meet demand when it's at its highest. It will also give you the opportunity to try out new models before you decide to buy.
4. Order extras & Engage with Rental Providers Early
It's generally a good idea to invest in the exact number of items you need - no more and no less. This keeps costs low because you don't have to deal with excess units that you don't actually need, and reduces congestion because you have enough to handle a normal workload.
However, you won't have a normal workload during peak season. During these times, you may want to have a few extra forklifts or another type of materials handling equipment. Schedule a rental in anticipation for your busy days so you have them available without the obligation to maintain them throughout the rest of the year.
5. Ensure Adequate Charging Infrastructure
Renting more batteries may require additional charging stations or more efficient chargers. Ensure you have the right setup in place to keep all your batteries charged and ready.
6. Incporporate Costs into Pricing Strategy
While flex battery rentals can be cost-effective during peak times, it's essential to incorporate these additional expenses into your pricing or cost absorption strategies.
7. Have a preventive maintenance plan for equipment
This is a tip to follow year-round, but it's especially helpful when you're busier than usual. When you have a plan to regularly inspect all equipment, perform preventive maintenance and responsibly replace items when they're at the end of their lifespans, your whole operation will work more smoothly. Facilities that follow a responsible equipment maintenance plan experience fewer unanticipated breakdowns and bottlenecks, thereby supporting a more efficient operation.
When you partner with Concentric's Dedicated On-Site Maintenance Team, an on-site technician can take ownership of your equipment maintenance plan, including any material handling equipment rentals you needed for peak holiday shopping season. Your technician is dedicated to your success, and will make repairs and recommendations as well as place orders for spare parts or additional rentals as needed.
8. Plan for the Off-Peak Season.
Once the peak season winds down, work with the rental provider to return excess units or transition to a lower rental tier. Review the season's operations, gather feedback, and identify areas of improvement for the next peak season.
By effectively leveraging flex forklift battery rentals, businesses can maintain operational efficiency during the peak holiday season without the long-term financial commitments associated with purchasing additional units. It's a smart way to remain agile and responsive to market demands.
Reach out to us today for all of your peak season battery rental needs.
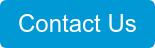