Material handling is a critical part of the American economy, but it can also be a dangerous line of work. In 2016, workers in transportation and material moving occupations endured 178,620 nonfatal workplace injuries or illnesses that resulted in days away from work, according to data from the U.S. Bureau of Labor Statistics.
Some of the most common types of injuries that occur in this industry involve forklifts. As such, safety should be the top priority for all facility managers. Various forklift safety accessories can create a safer work environment. These three forklift attachments are highly effective and can prevent dangerous situations from occurring:
Sensors that detect tip-over risks
The most common type of forklift accident is the tip-over. Many situations can lead to a forklift overturning, but no matter the cause, the results can be very dangerous and costly. Not only is the operator at risk for severe injury and even death, but so too are any other employees in the vicinity. Additionally, tipping over can damage the inventory the forklift was carrying, lift truck itself and any nearby equipment.
Sensors that constantly monitor forklift conditions, including speed and direction of travel, can help to reduce tip-over accidents. Other conditions sensors can be programmed to detect are fork height, load weight or mast tilt angle. When the sensors detect conditions that could lead to instability, it activates certain limits that the truck from becoming unbalanced. These controls might include implementing a speed cap or restricting the angle of tilt the mast can reach.
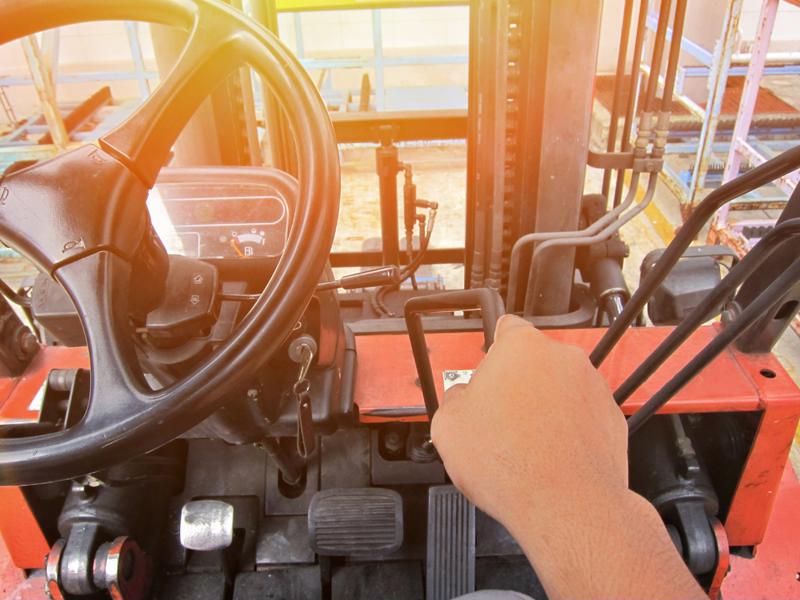
Sensor systems that detect dangerous situations can reduce forklift accidents in the workplace.
Anti-collision systems
Like tip-overs, forklift collisions can lead to damage and injuries. Equipment managers should invest in anti-collision systems, which can be installed in high-traffic or historically problem-prone areas, or onto the trucks themselves. In any case, the systems monitor a predetermined range for potential risks.
The zones that the systems monitor don't have to be uniform. Certain advanced anti-collision systems such as ELOKON's ELOshield, which made its U.S. debut at the 2018 MODEX trade show, according to DC Velocity, are equipped to monitor oddly shaped areas. If there's a hazardous polygonal area in your warehouse, the system can monitor it. When one truck gets dangerously close to another vehicle, a pedestrian or any other piece of equipment, the system alerts everyone in the area with visual and audible warning signals. It can also cause the truck to rapidly reduce its speed or even bring the vehicle to a complete stop.
Forklift safety isn't entirely the responsibility of the operator; pedestrians also must be aware of their surroundings and understand how their actions can put them in danger. To that end, anti-collision systems can be adopted by workers outside the driver's seat. When a pedestrian walks too close to a forklift, a connected tag that they carry or affix to their clothing begins to vibrate, letting them know that they need to move further away.
Light communications systems
Sometimes a relatively simple addition can make a much safer work environment. Light communications systems installed on the top or side of a forklift can go a long way toward giving pedestrians clear warning of where forklifts are located and in which direction they're traveling. A blue light shines onto the floor, letting anyone rounding a corner or coming from the other side of an aisle know that a truck is headed their way. Though not as technologically advanced as other material-handling innovations, warning lights are highly effective at improving visibility throughout the warehouse.
To begin making upgrades to your forklifts in order to reduce the risk of accidents, contact National Maintenance Services. We work with highly trained embedded technicians who can identify ways to improve your operations and maintain your equipment.